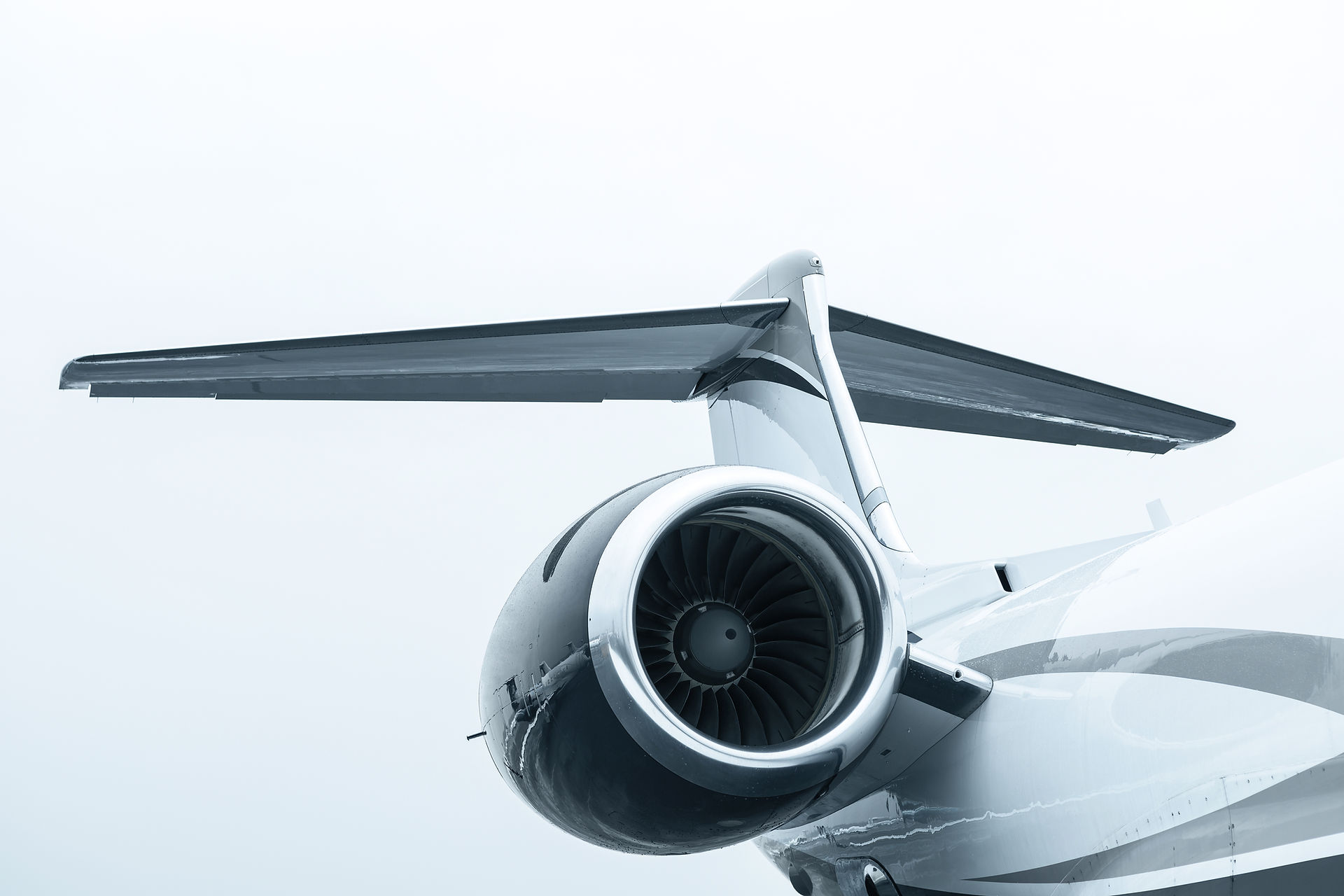
Ametek Airtechnology Group
The team made significant improvements in QCD. Customer Delivery Schedule Achievement improved by over 50% and increased time of test availability of 50%.
Quality of product testing improved by 100% with all test equipment being available at the time of use.
Cost also was reduced with a saving of £30k per annum

Having a ‘reset’ process for when the test is complete, ready for re-use. A SOP for process control and within the layout areas for receiving, exporting parts so as to cope with multiple and single part use. The teams also created analysis to show how families and groups of parts can be tested in sequence with each other. In this way the test area can be maximised for parts that need testing and in order of customer orders.
Project 1 Outcomes:
The team made significant improvements in QCD. Customer Delivery Schedule Achievement improved by over 50% and increased time of test availability of 50%.
Quality of product testing improved by 100% with all test equipment being available at the time of use.
Cost also was reduced with a saving of £30k per annum.
Ametek Airtechnology Group are a multibillion-pound business within the Aerospace, Train, Plane and MOD sectors.
The Project Team
The Team from various disciplines around the business including, QA, Warehouse, Engineering, Operations, Despatch, Test and Team Leader levels.
Team Training Overview:
The team used the 8 Problem Solving Disciplines (8D) the identify the ‘Real’ problem using Data from Measuring and Analysis Skills. Create ‘Root Cause’ analysis to potentially stop reoccurrence. Create solutions and trial them using the Plan, Do, Check, Act Approach. Implement a Measurable Method of Solution such as NRFT, FSU etc and Remeasure to show the areas of improvement within Quality, Cost and Delivery. All evidence and team meetings, charts and CI Boards are recorded to show marked improvements along with auditing for Visual Management and 5S.
Project Target: Reduce Test Turnaround by 50%
Method Example Project 1:
The teams were able to reduce Test Time, through organising the workplace area (Test Area) using 5s to have everything at hand, ready for use each time. The process of use and layout creating a sequence of lean processes to maximise the time of test without any increase in time through lost, faulty or missing equipment.